IPC-6012’s Significance In PCB Production
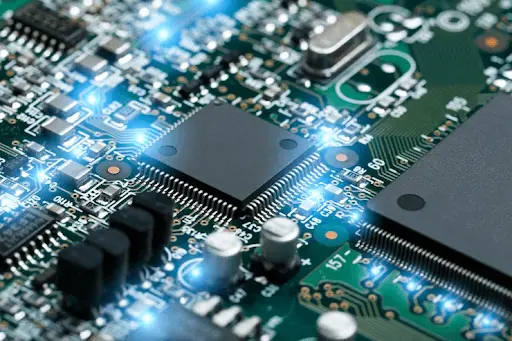
The PCB and electronics assembly sectors are served by the international trade group, the Institute of Printed Circuits (IPC). With a membership of more than 4,000 member firms, the IPC is an ardent organization devoted to the electronics sector. The IPC, established in the year 1957 and headquartered in Illinois, has produced a number of PCB standards that producers of PCBs are required to follow at all times.
IPC confirms the quality and excellence of manufactured PCBs and PCBA by imposing a few inspection rules. The IPC has several guidelines that PCB makers must follow while creating their PCBs. The IPC-6012 and the IPC-A-600 are the two main IPC guideline documents. IPC-6012 covers the stiff PCB qualification and performance requirements. IPC-A-600, on the other hand, discusses whether PCBs are acceptable.
Have you ever tried to design a PCB and sent it to a manufacturer only to discover that they couldn’t make it because you disregarded the laid down IPC standards? You are not alone; many PCB designers regularly deal with this issue. You must adhere to IPC standards to produce your boards without delays or complications. Hiring staff members that have completed IPC certification and training programs, such as IPC 6012 training, etc., can help with this.
IPC standards are important for several key reasons. First, designers and manufacturers can save time by using IPC standards while creating their goods. By undertaking IPC verification, designers and manufacturers can significantly reduce the time needed for rework during a recall event.
Additionally, careful attention to detail and a commitment to quality throughout the production process are required to develop dependable, safe, and high-performing pcbs. Printed circuit boards easily do this by following IPC specifications. Compliance with IPC standards is necessary for businesses to provide trustworthy, high-quality goods that meet or exceed client expectations. Companies stand to gain from increased product reliability and quality by following IPC standards.
IPC Assembly Specifications For PCB Production
There are numerous IPC standards that PCB manufacturers must always follow. But IPC-A-6012 is the most frequently employed and acknowledged standard, as was previously stated. IPC-A-6012 covers the Acceptability of Electronic Assemblies.
Rigid Printed Boards Qualification and Performance Specification (IPC-6012)
The HDI and passive/active pcb performance and qualification standards were established and defined by the IPC 6012 standard. These specifications define the categories of wooden boards while outlining the requirements that Class 1, 2, 3, and 3A wooden boards ought to fulfill.
A Performance Specification Is IPC-6012.
It is primarily a performance specification than the IPC-6012. The IPC-6012 sets the recommended requirements plus the criteria required for each Class of pcb because it is a performance specification.
Here are a few distinctive IPC-6012 requirements worth noting:
Dimensional
Printed circuit boards must adhere to the IPC-6012 minimum dimensions unless indicated on the specification or drawing.
Solderability
“Solderability” describes how quickly molten solder can moisten a metal. All batches of printed circuit boards must pass the solderability testing in accordance with IPC-6012 guidelines. IPC-6012 standards classify poor solderability as a serious flaw.
Every printed circuit board must pass a visual inspection. Before a product is released, a visual inspection or last-minute quality check is required. Unless otherwise stated, all panels are subject to visual inspection.
Conductor Size And Distance
The minimal air gap between the two adjoining copper features is called conductor width and spacing. The conductor and breadth gap typically needs to be less than 0.007 inches. Anything with a thickness of 0.007 inches or less is unacceptable.
Conductor Surfaces
For Class 2 as well as Class 3 printed circuit boards, pinholes and nicks are permissible in the voltage plane. However, their longest dimension shouldn’t be longer than 1.0 mm. Furthermore, no side should have more than four conductor surfaces.
Cleanliness
Cleanliness is essential to meet IPC-6012 requirements. Before applying the solder resist coating in this case, all printed circuit boards need to be clean. Contaminated, dirty boards shouldn’t be permitted to enter the marketplace. Both before and after applying the solder resist layer, cleanliness is essential.
Structural Integrity
All PCBs must adhere to several structural integrity requirements outlined in IPC-6012 standards. All printed circuit boards must adhere to structural integrity requirements based on IPC-6012 standards, particularly for thermally stress assessment test coupons.
Production Design Methodology
The procedures that should be used when designing PCBs for production are laid out in the IPC-6012 standards. In this case, the complete plot of land and the spacing requirements should fall within the suggested tolerances. The drill holes must also adhere to the necessary standards for size and quality. The parameters for the solder mask must also be within the advised tolerances.
The Performance Criteria Are More Specific.
The performance criteria are a little bit more precise for IPC-6012 standards. Users must think about what the supplier must essentially deliver when it comes to performance standards. Additionally, it describes the materials used and the testing the board underwent to demonstrate its operation.
In conclusion, IPC establishes IPC-6012 compliance to determine the specifications for printed circuit boards.